PhotonFanatic
Flashlight Enthusiast
Trying another light from Mokume Gane, a little bigger than the Kuukuu Mokume Killer; this light will have a 10440 Li-Ion battery, mini FluPIC driver with three levels of brightness, a Seoul P4, McR-13 reflector, mineral glass lens, O-rings, and split ring attachment point. The Molume itself is a three-color twisted bar, made from copper, brass, and nickel silver.
Here are some pics along the way:
Head with external threads, O-ring groove and milled slots for grip when turning the head.
Showing the internal threads to hold the Light Engine; there isn't a lot of metal between those two sets of threads! :devil:
Testing the mating of the head with the battery tube. The threads were lapped with diamond paste to smooth out the normally rough threads that Mokume produces--due to the difference in hardness among the three metals.
The battery tube has had its vertical and horizontal grooves milled into it. At the far left you can see the hole drilled for the split ring. The battery tube was then turned around and the finishing operation was milled to complete the bevel leading to the split ring.
Close-up of the split ring/bevel--note that the hole has not been deburred.
Next the head was completed by boring out the light exit hole, beveling the front of the head, and putting the 45-degree chamfer to the outside diameter.
This is the almost completed battery tube/head combo--just needs a little bevel where battery tube joins the head. Then it is on to the light engine machining and finally the finishing of the surface. While I don't plan to etch this light, I will be putting some sort of patina on it.
Here are some pics along the way:
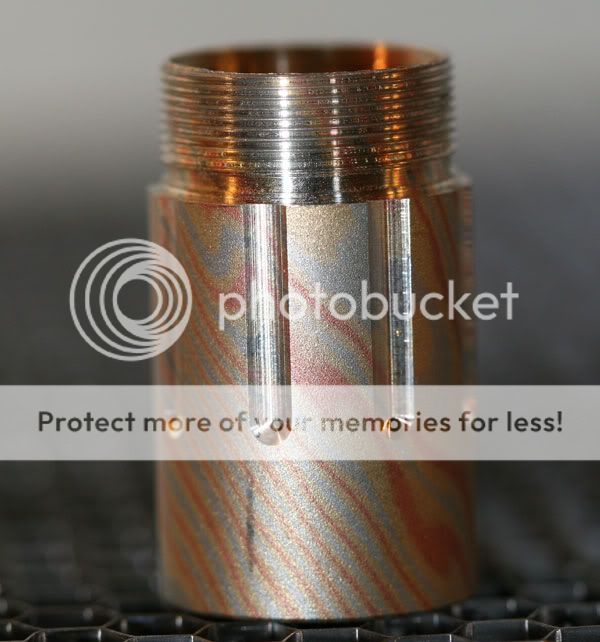
Head with external threads, O-ring groove and milled slots for grip when turning the head.
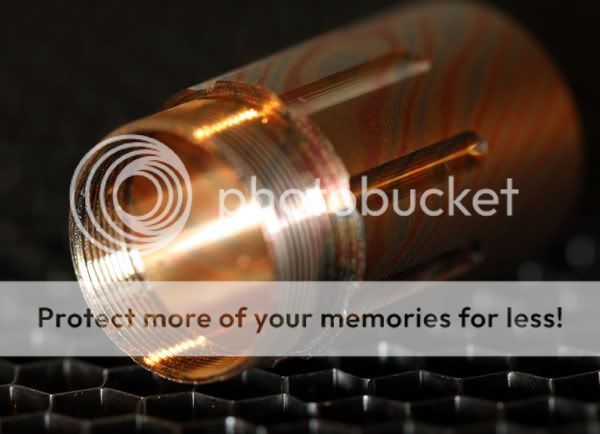
Showing the internal threads to hold the Light Engine; there isn't a lot of metal between those two sets of threads! :devil:
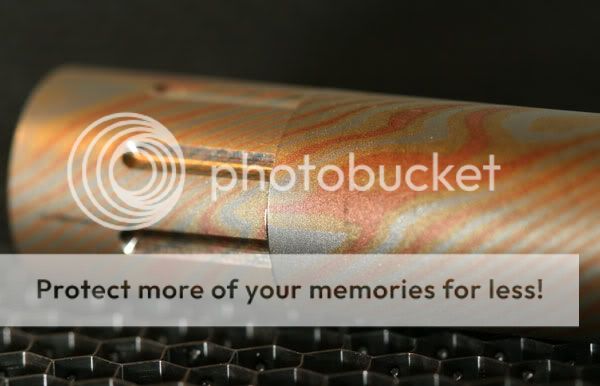
Testing the mating of the head with the battery tube. The threads were lapped with diamond paste to smooth out the normally rough threads that Mokume produces--due to the difference in hardness among the three metals.
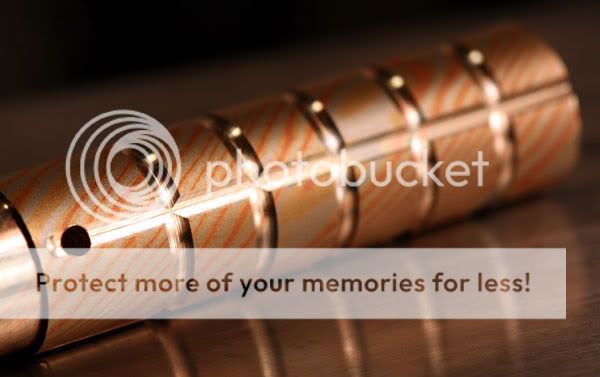
The battery tube has had its vertical and horizontal grooves milled into it. At the far left you can see the hole drilled for the split ring. The battery tube was then turned around and the finishing operation was milled to complete the bevel leading to the split ring.
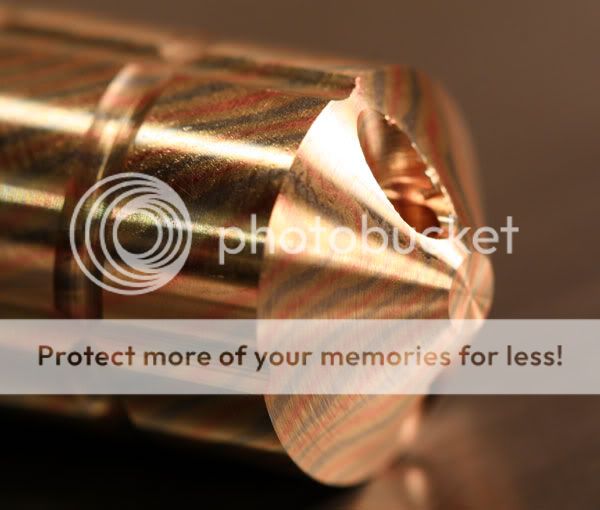
Close-up of the split ring/bevel--note that the hole has not been deburred.
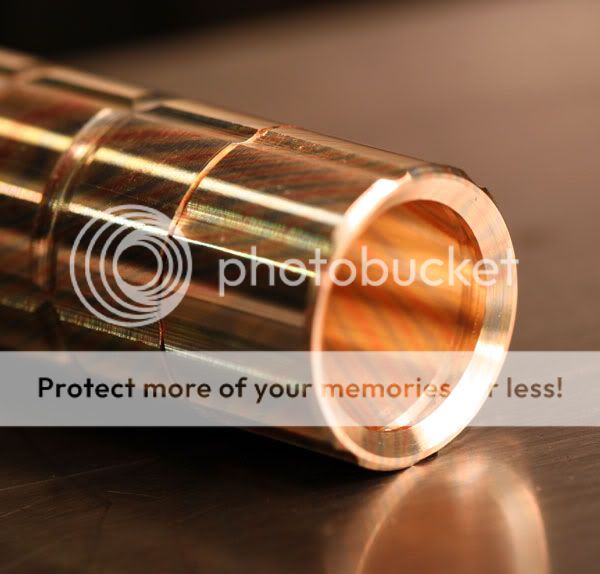
Next the head was completed by boring out the light exit hole, beveling the front of the head, and putting the 45-degree chamfer to the outside diameter.
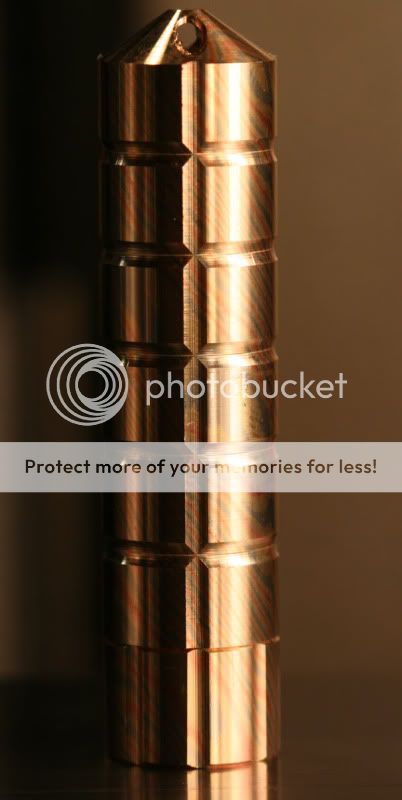
This is the almost completed battery tube/head combo--just needs a little bevel where battery tube joins the head. Then it is on to the light engine machining and finally the finishing of the surface. While I don't plan to etch this light, I will be putting some sort of patina on it.