I have been prototyping some new super light weight and small 900 lumen
P7 lights. I have tested several of the P7 lights and they are blowing away my HID's and so the HID's are going on Ebay for sale.
I am thinking of having a bunch of the parts made and then offer the parts as a do it yourself type thing with web site instructions on how to do it.
I don't have time to assemble lights and I would like to keep the prices as low as possible on the parts so people can get into high performance lights for way less than the silly prices being asked by some of the commercial light companies.
Anywho, I haven't decided if I am going to have the parts made yet. I would appreciate feedback on the design and if there is enough interest, I will have a machine shop run off 100 or so and see how it goes.
I already have a web store for my main business, so the parts sales aspect is already in place.
This link takes you to my bike lights page, the new light link is at the top of this page.
http://www.el34world.com/Misc/bike/BikesLights1.htm
I am still working on a cheap Li-On charger design that will charge battery packs, not individual batteries.
Thanks for any feedback.
Here's a shot of a scratched up prototype, just to give you an image.

I am thinking of having a bunch of the parts made and then offer the parts as a do it yourself type thing with web site instructions on how to do it.
I don't have time to assemble lights and I would like to keep the prices as low as possible on the parts so people can get into high performance lights for way less than the silly prices being asked by some of the commercial light companies.
Anywho, I haven't decided if I am going to have the parts made yet. I would appreciate feedback on the design and if there is enough interest, I will have a machine shop run off 100 or so and see how it goes.
I already have a web store for my main business, so the parts sales aspect is already in place.
This link takes you to my bike lights page, the new light link is at the top of this page.
http://www.el34world.com/Misc/bike/BikesLights1.htm
I am still working on a cheap Li-On charger design that will charge battery packs, not individual batteries.
Thanks for any feedback.
Here's a shot of a scratched up prototype, just to give you an image.
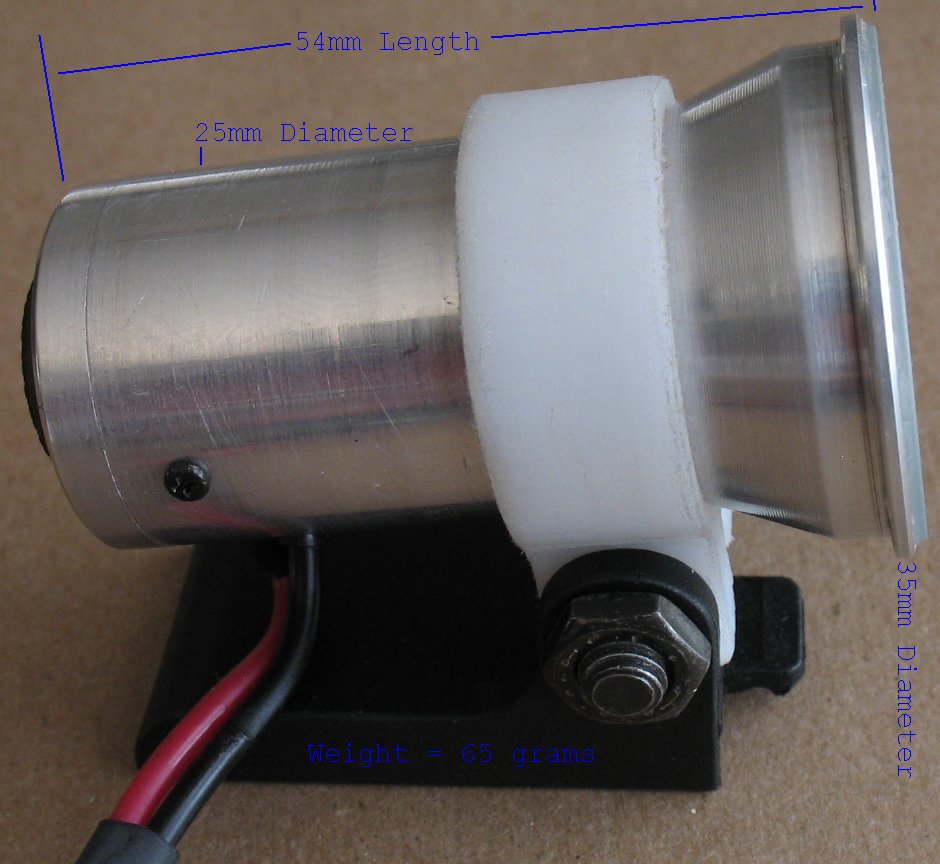