Hello,
I'm thinking about crafting a dive lamp, or to mod a old broken halogen lamp and I have some questions about cooling LED (especially with COB LED) dive lamps .
Which design is better for cooling ? Thin heatsink or thick heatsink (see picture below)? Of course it is probably related to led's power but is there a rule of thumb to choose a appropriate size?
With a thin heatsink design is there a risk that the LED warms the driver ?
Does anodizing affects thermal transfer, so is it better put the led on raw aluminum rather than anodized aluminum (of course with thermal paste or pad between)?
In Dive lightning library, Lucca Brassi posted an interesting concept of hole through metal enclosure for a better cooling, did someone tried it ?
Thanks
I'm thinking about crafting a dive lamp, or to mod a old broken halogen lamp and I have some questions about cooling LED (especially with COB LED) dive lamps .
Which design is better for cooling ? Thin heatsink or thick heatsink (see picture below)? Of course it is probably related to led's power but is there a rule of thumb to choose a appropriate size?
With a thin heatsink design is there a risk that the LED warms the driver ?
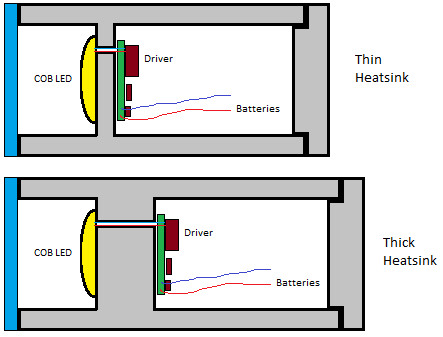
Does anodizing affects thermal transfer, so is it better put the led on raw aluminum rather than anodized aluminum (of course with thermal paste or pad between)?
In Dive lightning library, Lucca Brassi posted an interesting concept of hole through metal enclosure for a better cooling, did someone tried it ?

Thanks