jl.
Newly Enlightened
I've had my Nitecore D10 for about a month now and have loved it so much it has become my EDC. However, I twisted the head and it broke off!
I've only had it for a short time I hope that Nitecore will replace it under warranty as I think it should be a bit tougher than it is! It's broken where the knurling on the head meets the smooth section and the aluminium is very thin and I can only assume this is a manufacturing fault on my particular flashlight.
I've only had it for a short time I hope that Nitecore will replace it under warranty as I think it should be a bit tougher than it is! It's broken where the knurling on the head meets the smooth section and the aluminium is very thin and I can only assume this is a manufacturing fault on my particular flashlight.



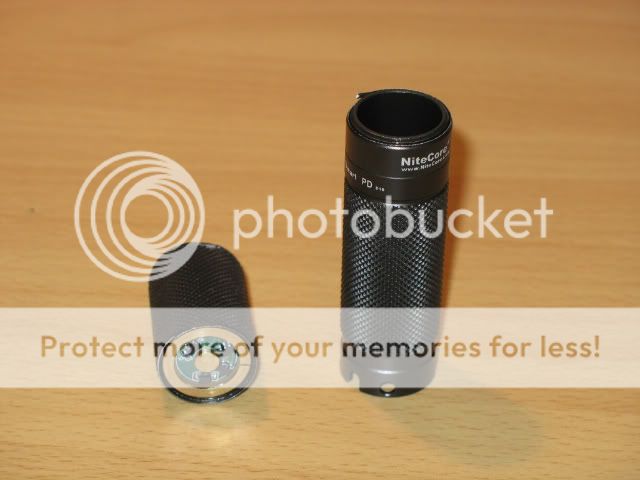

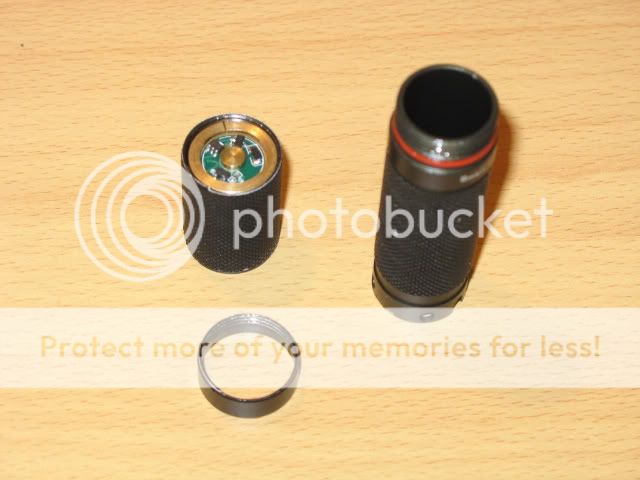


Last edited: