Mkala
Newly Enlightened
Hi all :wave:
After searching and tested some G4 replacement lamps, I decided to try to build my home made solution
The target light fixture (is it the name ?) is this :
This is a lamp for dinning table, which have 7 lamps at 20W each, total 140W plus losses in electronic PSU it should be about 150W.
20W G4 lamps mean about 220lm, it should be hard to achieve this with LED. The main problem is thermal dissipation in space constrained and virtually closed environment (the top of glass "cups" are closed, meaning heat will stay here...).
The second problem is space for electronic, it have to be really small...
First, ordered some heat sinks, mounted a cree XP-E high CRI (>90). The main drawback is light output, only 80lm at 350mA.
For this application, I target a current of 550mA, witch result at 120lm. Yes it is a bit low, but halogen bulbs radiate at 360°, this result in a lot of losses in this application.
First prototype :
The electronic is from another LED bulb, I have to build a custom circuit :
Advices welcome.
Now I should finish electronic design, build 2-3 LED to validate lighting output. If too low, I can increase the current, but I should take care of LED temperature (which is hard to be sure, without IR thermometer)
The other solution is to replace the high CRI LED chip with another warm white chip, more efficient but with bad in color rendering..
Prototype inside light fixture :
See u
After searching and tested some G4 replacement lamps, I decided to try to build my home made solution
The target light fixture (is it the name ?) is this :
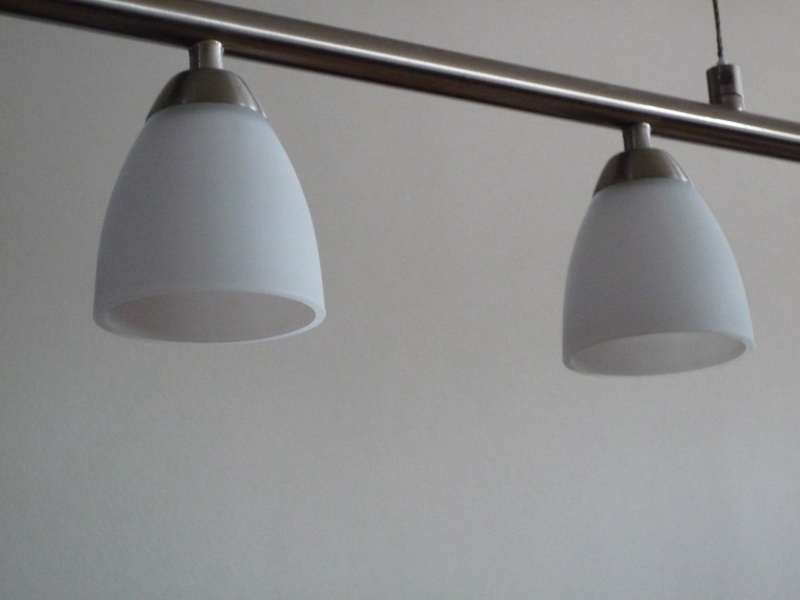
This is a lamp for dinning table, which have 7 lamps at 20W each, total 140W plus losses in electronic PSU it should be about 150W.
20W G4 lamps mean about 220lm, it should be hard to achieve this with LED. The main problem is thermal dissipation in space constrained and virtually closed environment (the top of glass "cups" are closed, meaning heat will stay here...).
The second problem is space for electronic, it have to be really small...
First, ordered some heat sinks, mounted a cree XP-E high CRI (>90). The main drawback is light output, only 80lm at 350mA.
For this application, I target a current of 550mA, witch result at 120lm. Yes it is a bit low, but halogen bulbs radiate at 360°, this result in a lot of losses in this application.
First prototype :
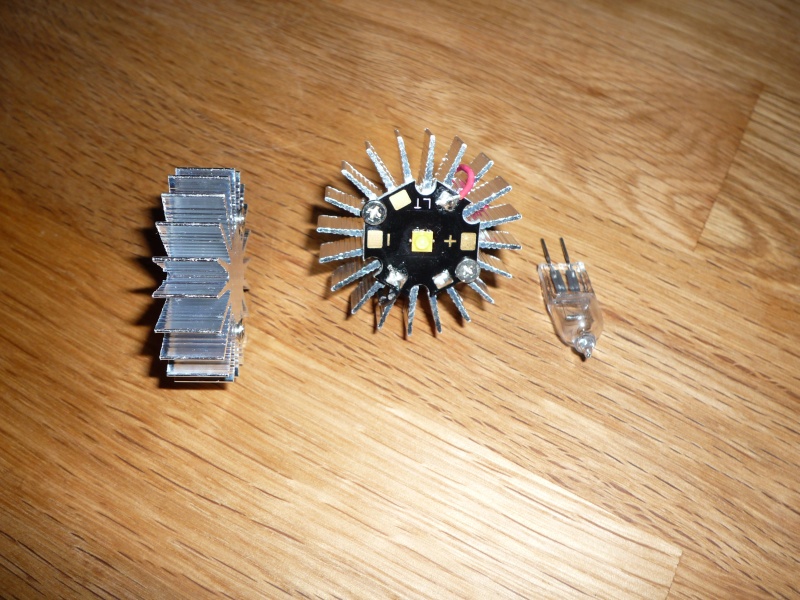
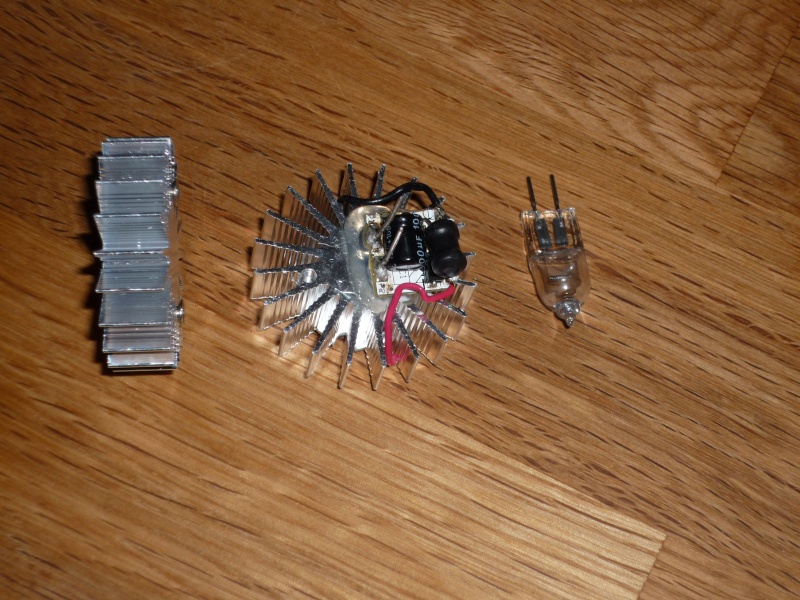
The electronic is from another LED bulb, I have to build a custom circuit :
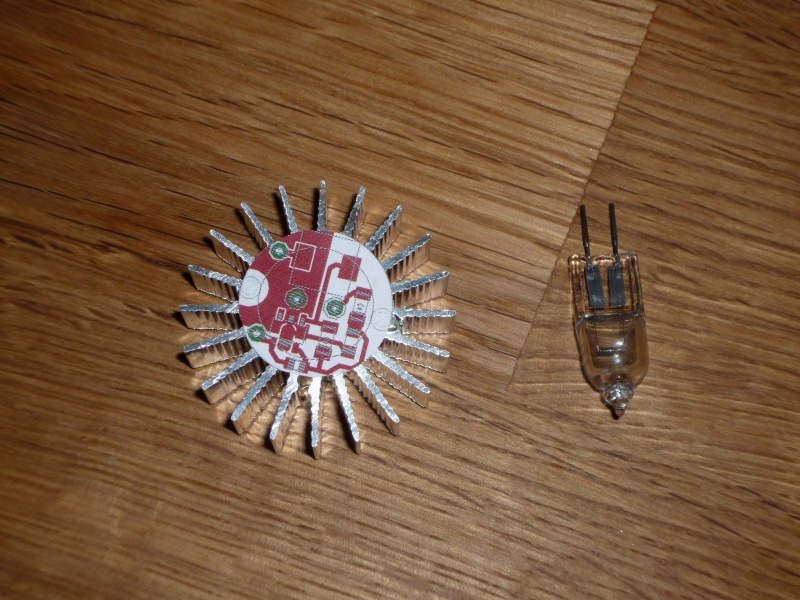
Advices welcome.
Now I should finish electronic design, build 2-3 LED to validate lighting output. If too low, I can increase the current, but I should take care of LED temperature (which is hard to be sure, without IR thermometer)
The other solution is to replace the high CRI LED chip with another warm white chip, more efficient but with bad in color rendering..
Prototype inside light fixture :
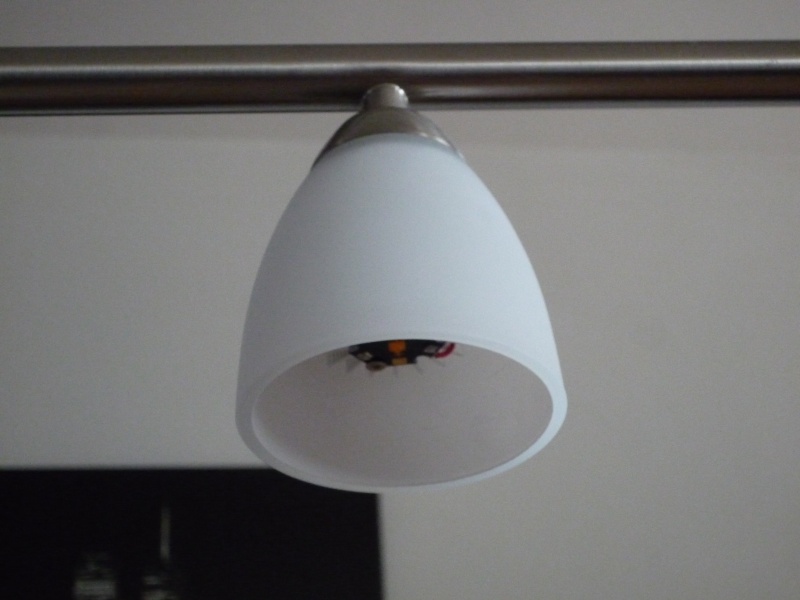
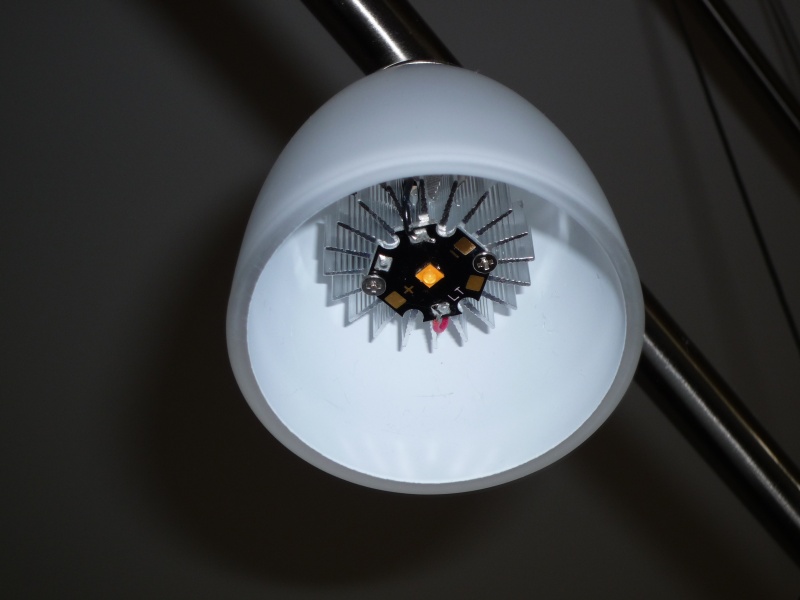
See u
Last edited: