VanIsleDSM
Enlightened
I just downloaded google sketchup yesterday. At first it was odd to get used to, but I seem to be getting the hang of it now. I knew I needed to start doing 3D models to make the machining work easier, rather than just figuring it out as I go along. I learned a lot doing this, now I'm eager to make some more models, but I think I'm gonna go have a whirl at machining the head of this thing right now. I'm not entirely sure how long to make the body yet, depends on which driver I decide to use. I ordered 3 different single cell drivers to test them all out and decide which I want to use. The different heights of these drivers will decide how long the body has to be.. that and the fact that DX didn't list all the specs for the clicky switches I ordered.
I've got a CREE R2 WH I'll probably put in here. Also picked up a couple of those 19mm AR coated glass lenses from KD, but I'll have to shave them down to ~18mm to work.
Planning to silicone the lens in at the front, and silicone the tailcap rubber protector in as well. Then there's the 3 O-ring seal designed to work with 21mm OD 18mm ID O-rings. I used this chart to help me design the specs for the O-ring seals: http://www.norseal.com.au/tolerances/ormach.htm (Thanks Dom)
Hopefully that'll be enough that I can submerge the light without any problems. Not for diving, but just some snorkeling maybe. Once it's built I'll take it down to 20ft or so with no battery to see if it comes up dry.
As for the threads, they don't really go anywhere. I don't know how to make them helical yet, I think you need to write script and such. I'm happy with the straight around threads, they do well enough for measurement. They're 24TPI.
I've got a CREE R2 WH I'll probably put in here. Also picked up a couple of those 19mm AR coated glass lenses from KD, but I'll have to shave them down to ~18mm to work.
Planning to silicone the lens in at the front, and silicone the tailcap rubber protector in as well. Then there's the 3 O-ring seal designed to work with 21mm OD 18mm ID O-rings. I used this chart to help me design the specs for the O-ring seals: http://www.norseal.com.au/tolerances/ormach.htm (Thanks Dom)
Hopefully that'll be enough that I can submerge the light without any problems. Not for diving, but just some snorkeling maybe. Once it's built I'll take it down to 20ft or so with no battery to see if it comes up dry.
As for the threads, they don't really go anywhere. I don't know how to make them helical yet, I think you need to write script and such. I'm happy with the straight around threads, they do well enough for measurement. They're 24TPI.
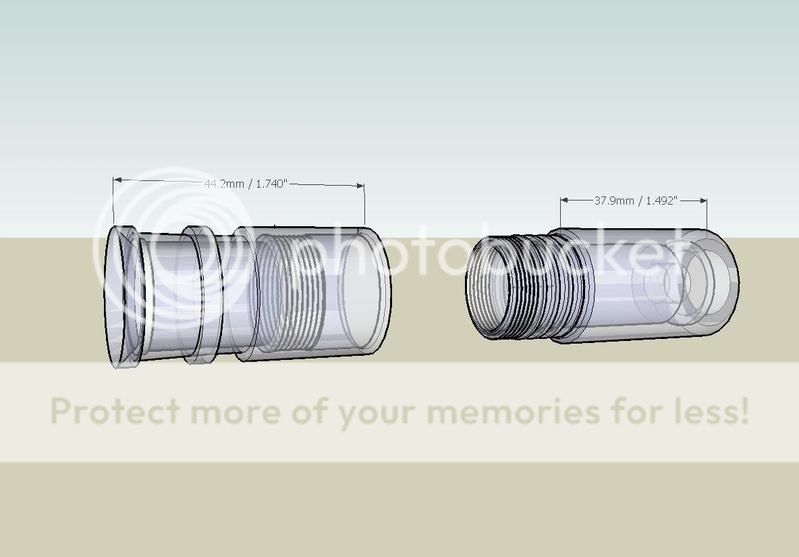



Last edited: