Some of you might recognize one of these units.
It's a typical multifunction hobby charger.
It's a great investment to the avid flashlight enthusiast as it can pretty much intelligently charge any battery or pack we'd have in our arsenal, from NiCD to LiFepo4. This particular model can be had on the Bay for about $50. I power it with an IBM laptop adapter that gives me plenty of voltage and current for most all my charging needs. 16v 4.5a to be exact.
One disadvantage is that it has but a single main output. This is not a problem for charging assembled packs that are designed to have the cells gang charged, but when you want to top off your set of Li-Ions so that your ROP or Mag 11 is ready to rip later on, you are pretty much limited to doing it one cell at a time.
If you can connect more then one at a time, you can charge them together, but as most battery geeks will tell you, better they each get their own attention. I've noticed the new LiFepo4 cells in particular can be sensitive, yielding different state of charge readings, fresh of the charger when charged together in series.
Most of the good hobby chargers will feature these special connectors, designed to establish control over each cell in a specially made lion/lipo/life pack. The pack will have a special charge connector to plug into these sockets.
Using grade school arts and craft skills, and some basic soldering skills, I have exploited this feature, effectively turning my charger into bank charger.
Here I have a set of 3 LiFe cells charging using the Balance charge function.
I took 4 C-Cell battery holders, cut them in half and glued them to a sheet of acrylic spacing the halves to accommodate 65mm cells.
I then wired the leads and the charge connector across this terminal strip. It has some nice lugs for me to connect my chargers alligator clips to while selecting the number of cells I wish to charge. As labeled, the Common Negative is the the left. Then from left to right I can select 1s, 2s, 3s, and 4s.
The festivities do not end there. As the cradle is sized for 65mm cells, it can also be used to bank charge 18650 lions. Seen here it's topping off my IMR for my EDC. You can unplug the balance connector and select 1s for single cell operation.
NOTICE: Make sure you read your chargers instruction manual, and double check your connections. As you are manually selecting your cell configuration there is a margin for error, and some chargers REALLY won't appreciate being hooked up wrong. For example, my chargers manuals warns that you might damage it, if you attempt to start a charge with the balance connector plugged in, but without the alligators connected properly.
Today I want to make a cradle to accommodate my shiny new AW IMR26500 cells that I just got in the mail to power my Megalennium 2x26500.
The ingredients are: one charge connector, a 3 point terminal strip, 2 C-Cell holders, and piece of acrylic.
Acrylic is pretty easy to work with. In Canada you can usually purchase it from your local Home Hardware for not lots of money.
To cut it you use a metal straight edge and a sharp knife. I'm using a pen knife.
When you figure out where you want to make your cut you run the knife along the straight edge to give it a nice score mark. If you can, run it over a few times.
Once you have your nice score mark, simply locate the mark along the edge of your desk or work bench like so, and snap it off.
Easy Peasy.
I originally attempted to construct these units using Hot Glue, aka: Glue Gun Glue. This did not work very well. Though it seems to stick to acrylic really well it did not hold up in use. The terminal strip on my 2x50mm cradle came loose, and the first two most used slots on my 2x65mm also fell apart during a charge.
I rebuilt the units using epoxy, it really is the best way to go for this setup.
Once we get it all together, it's ready for wiring.
This step will require basic soldering skills. If you are not confident soldering, I recommend lobbying the services of someone who is.
After all, sloppy work here could cost the lives of your batteries or your charger, and who knows what other collateral damage.
If you are new to soldering and can do a decent job, this may very well be a good beginner project. Just make sure to check and double check your work before using it, and maybe run a multi meter over it checking for continuity and resistance to confirm there are no cold solder joints. Also, if you are using the same kind of terminal strip as I am, watch out when you solder to the lug that is also used for mounting as it may soften the glue and come loose on you.
TIP: Soldering is like buttering toast. You use the knife the apply the cold butter to Hot toast, causing the butter to melt into the toast. You DO NOT, use a Hot knife to melt butter onto cold toast.
The idea with soldering is that you are using the iron to heat up the lug and the wire, then touch the solder to it, thereby the heat of the lug and wire causes the solder to melt and fuse to it. A common beginner mistake is to melt the solder with the iron and attempt to apply it. The correct method will almost always assure a good solder joint.
Here is the Wiring Diagram provided in the chargers manual. It lays out for you, pretty clearly (at least to an experienced tech like Me), how to wire up our charge connector. I imagine your charger manual might also feature such a schematic. This particular schematic SHOULD apply to most chargers as the balance Charger connection is a Industry Standard.
Here is the finished product. I used the centre lug as the common negative, and the adjacent lugs on either side for 1s and 2s connections, then labeled it as such.
If you prefer, feel free to stick to a more linear layout, it's jsut tech instinct to assign the common negative to the mounting lug.
The terminal strip I used is alot smaller then the one use on my 65mm 4s cradle, so I will use caution to make sure the alligator clips do not touch each other or any contacts they are not supposed to.
When sourcing out charge connectors, I recommend getting some that can accommodate the maximum amount of cells you may be building a cradle for. Chances are they will come in a lot.
I got a 10 pack for about $5.
The sockets in my particular charger are backwards compatible, and don't much care how many cells are plugged in at a time, as long as they are in proper order. You can remove extra pins from the connector and tailor it to your needs.
In my case, I bought a lot of 4s connectors off the Bay, and removed two pins to make a 2s connector, and my charger doesn't' mind that it is plugged into the 4s slot.
Here I have successfully built a 2 bank charger for my IMR cells.
All parts were sourced from Ebay:
The Battery holders were about 6 for $5.
The connectors were about 10 for $5. Search "balance charger plug".
I forget how much I paid for the Acrylic at Home Hardware.
And the terminal strip could be found in lots for about $1 each. Search: "terminal strips".
One of these cradles likely costs less then 5 dollars. Once you have a lot of supplies as I do, you could build all sorts to accommodate your various battery charging needs.
Seen here I chopped a single D-Cell holder, into 3, to create a cradle to charge five 1/2D cells, for dropping 6volts into a 3D Mag, for running Magcharger or Wa1160 bulb.
IMPORTANT SAFETY NOTICE:
These designs have no official safety certification, as such their limits are unknown. It is up to the individual user to verify and monitor their safe operation. Many CPF members will have the experience necessary to construct and safely use these units, and this post is for their benefit.
If used incorrectly or overloaded they could very well pose a fire hazard. For this reason, I advise you build and use one of these units at your own risk.
Unless you have a good idea of the limitations of the particular components used in one of these builds I would recommend limiting the applied current battery holders with stock leads to 1amp. As the leads that came with my battery holders are very flimsy, chances are this current spec will be safe for any other variation of this build.
In use I've noticed some mild warmth coming from the battery holder leads when 2amps is applied. This does not last long, as no matter what current level I would set, the smart charger would throttle down the current to about 1.1amps, and did not seem to want to push any more then that through the flimsy leads.
I can only imagine the charger detected insufficient plumbing and compensated.
Upgrading and Revisions.
If you like this design, and use it regularly . . . AND are confident with your soldering skills, you may consider upgrading the leads to up the charge rate and assure an overall safer operation. I found this necessary as I was unable to get the charge rates I wanted with the stock battery holder leads.
This requires some quick and confident solder welds as the plastic of the holder is likely to melt very easily.
I'm upgrading my cradles using 18 gauge solid wire. The solid wire was chosen mostly for the fact that I already had some on file. Solid wire is capable of conducting more efficiently then stranded wire. As these cradles have a solid frame and don't really need to be shock rated, it's not a bad idea.
18 gauge wire is rate for 3 amps conservatively, and due to the very short distance and low voltages it could easily handle more in this application.
If you are looking to go up to a 10 or more amp charge I would consider using 14 gauge while also rigging it to bypass the stock battery holder contacts as seen here.
Upgrading the positive contacts, I pushed a stripped section of the wire though the battery holders contact holes and bend the exposed section.
I then pulled the wire back and made a quick solder weld to the contact.
This is the part where you have to be careful as the heat for the weld has likely started the plastic melting regardless of how fast you were.
A "tool" handy for this procedure is some "parts chiller" Basically a freezing action spray.
Once I made the weld, while carefully holding everything in place, I took the chiller and sprayed it onto the spot where I had made the weld, solidifying the plastic before it could slip and ruin the holder. You would otherwise have to hold the wire in place until everything cooled down.
If you don't have any boutique parts chiller, you can just use computer "air spray" tilting the can sideways so that the raw liquid sprays out. This is pretty much the same thing as parts chiller.
The other option, if you wish to avoid soldering all together, is once you have the bent wire in place on the inside of the battery holder contact, so simply glue the wire in place on the outside of the holder. I have not tried this personally, but with the right glue and proper technique it could be a good idea.
To make the negative contact you pretty much go through the same motions. The difference being that you would pinch the negative wire on the end of the spring like so. This would bypass the spring avoiding any dependency the circuit has on its quality or conductivity.
Afterwords, as the spring offers some thermal isolation from the plastic, it is considerably easier to apply solder without the risk of meltdown.
Once again, if you wish to avoid soldering, you can just pinch the wire onto the end of the spring without the need for solder.
Mind you, the solderless methods are likely to work with solid wire only.
Here we have the revised finished product. I like how the solid wire allowed me to shape it into a more uniform layout.
As discussed in this thread, these particular methods using balance charging systems might be somewhat redundant.
In the case of the 2x50mm cradle, a parallel system might be a better and less complicated way to go.
On the other hand, I find balance charging method advantageous in the 4x65mm cradle when I wish to hit more then 2 cells with a high rate charge. As my particular charger is limited to about 4 amps due to the powersupply used, I would be unlikely to hit 4x26650 LiFe cells with a 1C charge using the parallel method.
The Lux Luthor Magnet Method.
Since the creation of this threat, Lux Luthor brought to my attention another great way in which to utilize the Balance Charging system.
I've decided to try my hand at it.
If you live in Canada, you are likely familiar with the Home Hardware. My local A&J Home Hardware on Bouchard street in Sudbury can be a modders paradise, as they will custom cut you wire or pipe, have a workbench where they help you rough fit projects, and have the stock consistency of a nation wide chain store.
In their limited stationary supply section I was delighted to find they stock just the perfect kind of magnet we need for this project.
As this is a nation wide chain, these magnets should be available, (if by special order) at any home hardware across Ontario, and even Canada I would imagine.
This package cost $7.49cdn +tax.
As you can see, I constructed a 4S harness using 6 magnets.
Five for the BC connector (Balance Charge) and the common Negative;
and one for the floating Positive:
This idea is, you can snap on as many BC connector leads as you need to match your cell count.
Seen here, I have snapped together 3 cells for the charge. The Blue 3s wire being the last in the chain, snapping the floating posative onto the end of that chain, and omitting the Green 4s lead.
The insulated side of the battery seems a good place to snap the omitted lead magnet. It should stay out of trouble there.
With the remaining Magnets, I soldered up some parallel jumpers so I can use that particular method of charging for a pair of cells.
In this configuration, the omitted magnets are just all snapped together in their standby positions on the negative common side, while the BC connector is not plugged in.
The tricky part of the rig is the soldering. Too much heat applied to the Magnet can strip it of its magnetization rendering it useless. I've known this for a while. It's common knowledge among competent guitar techs that the use of high output soldering guns has been known to demagnetize electric guitar pickups.
Lux has mastered it, and has dropped tips among the forum. I myself have been soldering for over 16 years, and have the right equipment, so though reluctant to damage the magnets, I figured I could handle it.
The trick is to be quick, avoiding to much iron time on the magnet. You pretty much have to know how to solder and have decent experience doing so.
Refer to the "Butter on Toast" tip mentioned earlier in the thread. In this case, imagine using a blow torch to heat the bread just enough so that the butter melts into it, but without actually toasting it.
The method is something to be seen. I have made this HD video to illustrate.

If you can do the motions as seen here, you should be able to pull it off.
What you are seeing is:
A: I "tin" and preheat the wire for soldering,
B: I tin and preheat the magnet surface ",
C: I fuse the preheats and tinned parts together,
D: I quickly spray some "chiller" on the magnet to remove all access heat.
Tinning in the process of pre-fusing some solder onto the surfaces to be connected, as you would with contact cement glue, or even epoxy.
It's pretty much a mandatory prerequisite to making a good solder joint.
For tools:
- I have a set of jaws or "helping hands" to hold everything,
- A 35watt soldering iron. Note the medium flat tip used. Too sharp a tip might not spread the heat evenly. To wide may spread it too much making it hard to focus your
heat and overheating the magnet. The right tip could make or break this joint, you should be good with a fine tip though. A 35-45 watt iron with a med flat tip is pretty much a swiss army knife of irons to those who can use them well. DO NOT, use a solder gun!
- Some FINE standard Rosin Core solder. Nothing special but the size. Too thick could flood your joint making for a sloppy work.
- Parts chiller. The chiller has been discussed already, look for the pic of the can.
I was able to pull this off in one shot with no damaged magnets.
If you are not confident doing this, I would practice on some random pieces of metal. Maybe try soldering to the edge of a penny as they are about the same mass as the magnets, just keep in mind, It will take about half the time to fuse to the magnet as it would to the penny. I would recommend soldering to the edge of the magnets as it will take longer for the heat to spread across then it would if you soldered to middle. For soldering the common negative, fuse the main lead and the BC lead together before welding to the magnet so that you only have one joint to make.
Last but not least, mind the polarity. When you stack the magnet, they will only snap together one way, if you want your wires to be oriented a certain way, best to figure out how they will snap together before making the connections.
ENJOY !
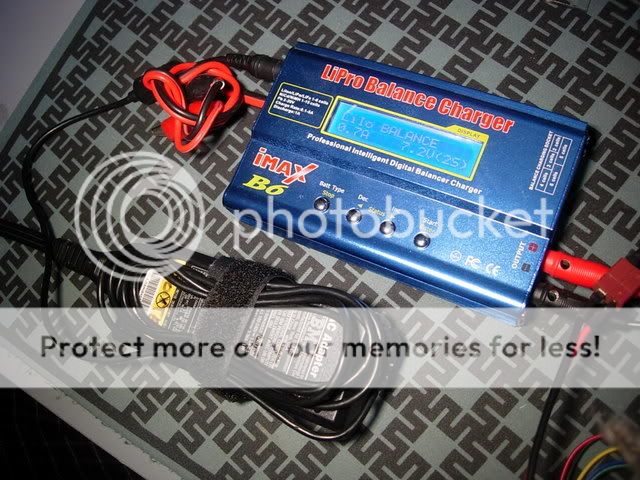
It's a typical multifunction hobby charger.
It's a great investment to the avid flashlight enthusiast as it can pretty much intelligently charge any battery or pack we'd have in our arsenal, from NiCD to LiFepo4. This particular model can be had on the Bay for about $50. I power it with an IBM laptop adapter that gives me plenty of voltage and current for most all my charging needs. 16v 4.5a to be exact.
One disadvantage is that it has but a single main output. This is not a problem for charging assembled packs that are designed to have the cells gang charged, but when you want to top off your set of Li-Ions so that your ROP or Mag 11 is ready to rip later on, you are pretty much limited to doing it one cell at a time.
If you can connect more then one at a time, you can charge them together, but as most battery geeks will tell you, better they each get their own attention. I've noticed the new LiFepo4 cells in particular can be sensitive, yielding different state of charge readings, fresh of the charger when charged together in series.
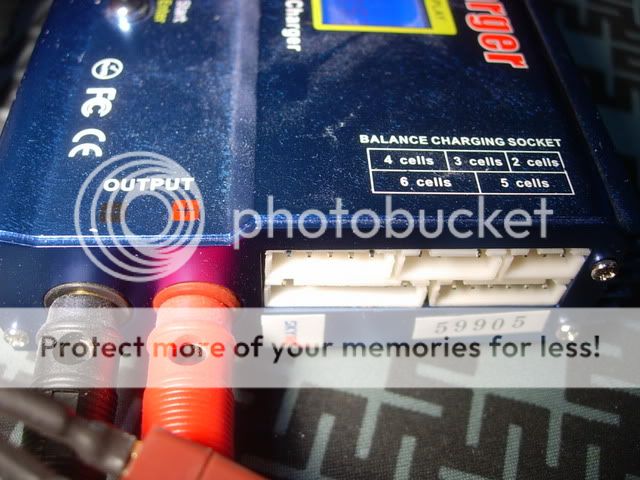
Most of the good hobby chargers will feature these special connectors, designed to establish control over each cell in a specially made lion/lipo/life pack. The pack will have a special charge connector to plug into these sockets.
Using grade school arts and craft skills, and some basic soldering skills, I have exploited this feature, effectively turning my charger into bank charger.
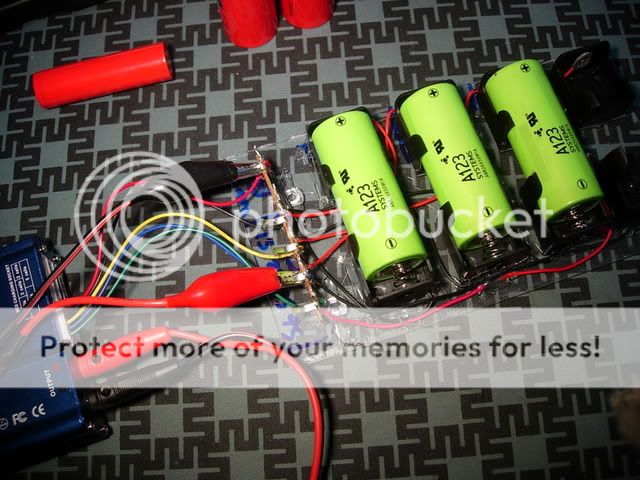
Here I have a set of 3 LiFe cells charging using the Balance charge function.
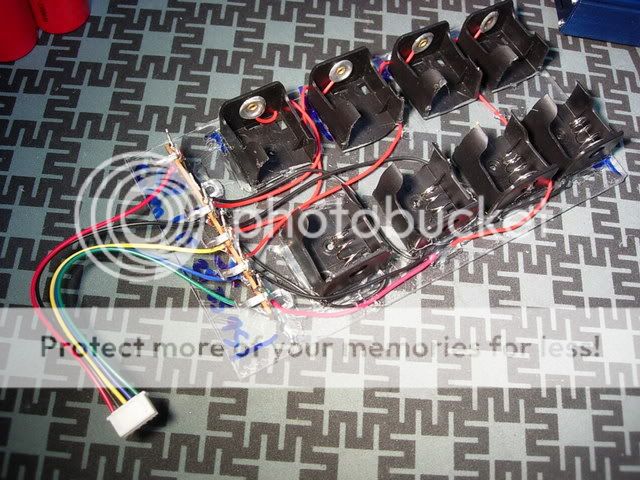
I took 4 C-Cell battery holders, cut them in half and glued them to a sheet of acrylic spacing the halves to accommodate 65mm cells.
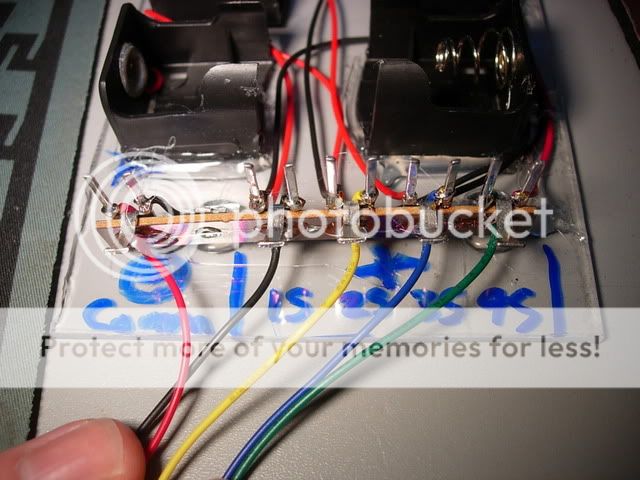
I then wired the leads and the charge connector across this terminal strip. It has some nice lugs for me to connect my chargers alligator clips to while selecting the number of cells I wish to charge. As labeled, the Common Negative is the the left. Then from left to right I can select 1s, 2s, 3s, and 4s.
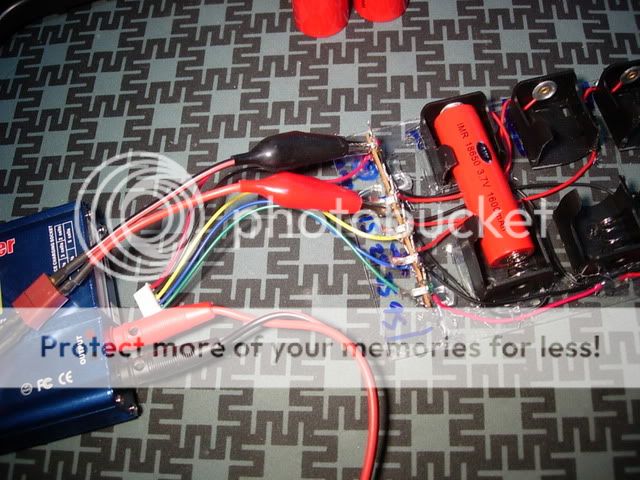
The festivities do not end there. As the cradle is sized for 65mm cells, it can also be used to bank charge 18650 lions. Seen here it's topping off my IMR for my EDC. You can unplug the balance connector and select 1s for single cell operation.
NOTICE: Make sure you read your chargers instruction manual, and double check your connections. As you are manually selecting your cell configuration there is a margin for error, and some chargers REALLY won't appreciate being hooked up wrong. For example, my chargers manuals warns that you might damage it, if you attempt to start a charge with the balance connector plugged in, but without the alligators connected properly.
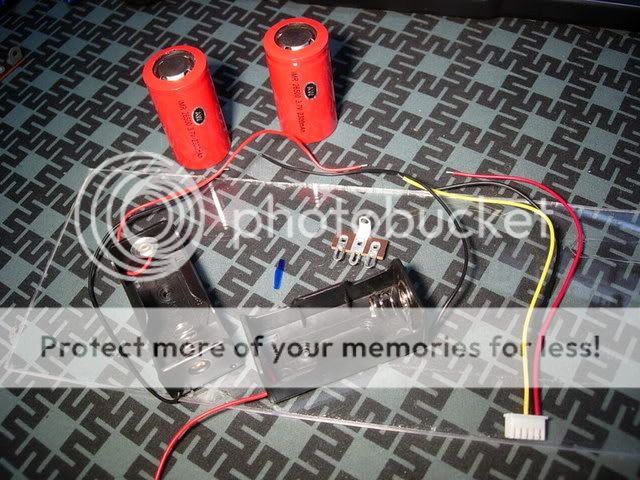
Today I want to make a cradle to accommodate my shiny new AW IMR26500 cells that I just got in the mail to power my Megalennium 2x26500.
The ingredients are: one charge connector, a 3 point terminal strip, 2 C-Cell holders, and piece of acrylic.
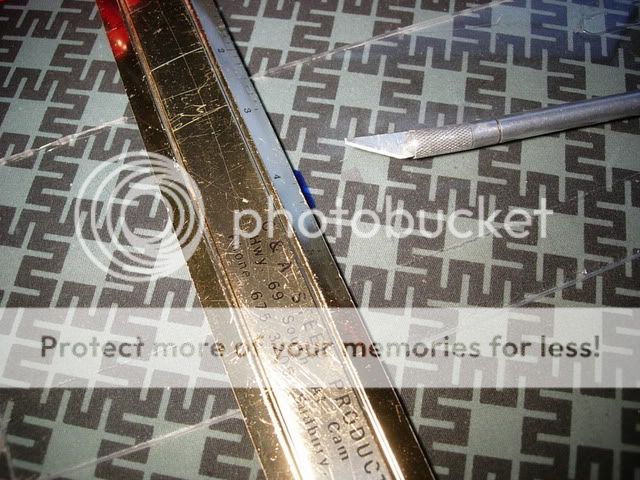
Acrylic is pretty easy to work with. In Canada you can usually purchase it from your local Home Hardware for not lots of money.
To cut it you use a metal straight edge and a sharp knife. I'm using a pen knife.
When you figure out where you want to make your cut you run the knife along the straight edge to give it a nice score mark. If you can, run it over a few times.
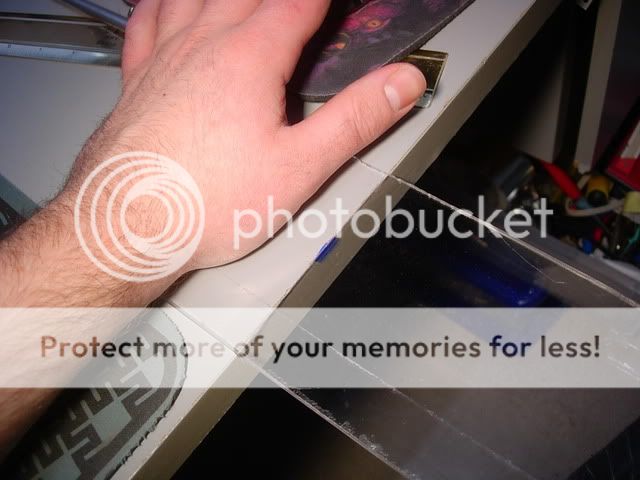
Once you have your nice score mark, simply locate the mark along the edge of your desk or work bench like so, and snap it off.
Easy Peasy.
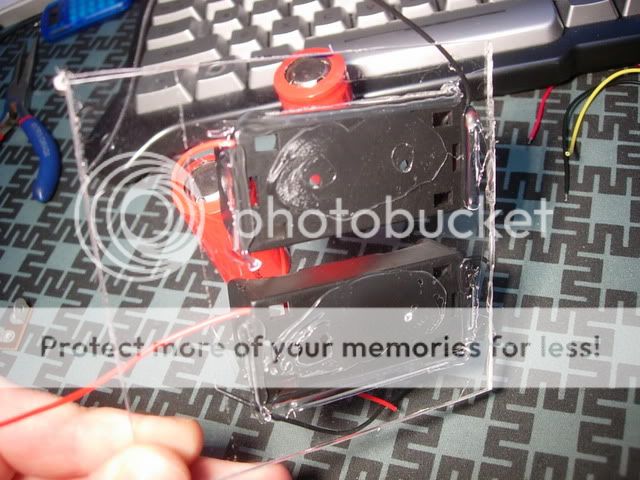
I originally attempted to construct these units using Hot Glue, aka: Glue Gun Glue. This did not work very well. Though it seems to stick to acrylic really well it did not hold up in use. The terminal strip on my 2x50mm cradle came loose, and the first two most used slots on my 2x65mm also fell apart during a charge.
I rebuilt the units using epoxy, it really is the best way to go for this setup.
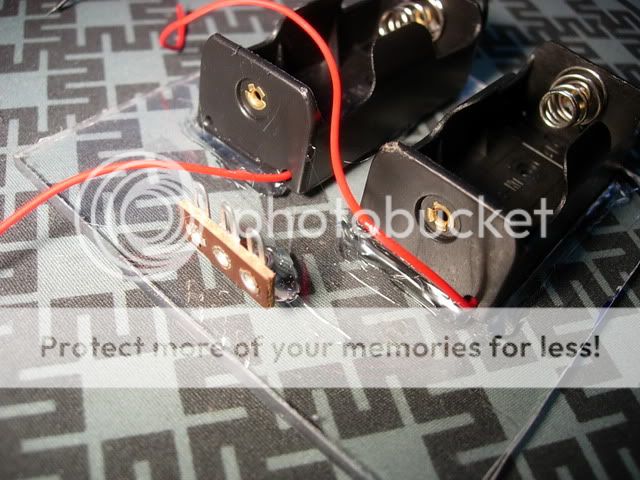
Once we get it all together, it's ready for wiring.
This step will require basic soldering skills. If you are not confident soldering, I recommend lobbying the services of someone who is.
After all, sloppy work here could cost the lives of your batteries or your charger, and who knows what other collateral damage.
If you are new to soldering and can do a decent job, this may very well be a good beginner project. Just make sure to check and double check your work before using it, and maybe run a multi meter over it checking for continuity and resistance to confirm there are no cold solder joints. Also, if you are using the same kind of terminal strip as I am, watch out when you solder to the lug that is also used for mounting as it may soften the glue and come loose on you.
TIP: Soldering is like buttering toast. You use the knife the apply the cold butter to Hot toast, causing the butter to melt into the toast. You DO NOT, use a Hot knife to melt butter onto cold toast.
The idea with soldering is that you are using the iron to heat up the lug and the wire, then touch the solder to it, thereby the heat of the lug and wire causes the solder to melt and fuse to it. A common beginner mistake is to melt the solder with the iron and attempt to apply it. The correct method will almost always assure a good solder joint.
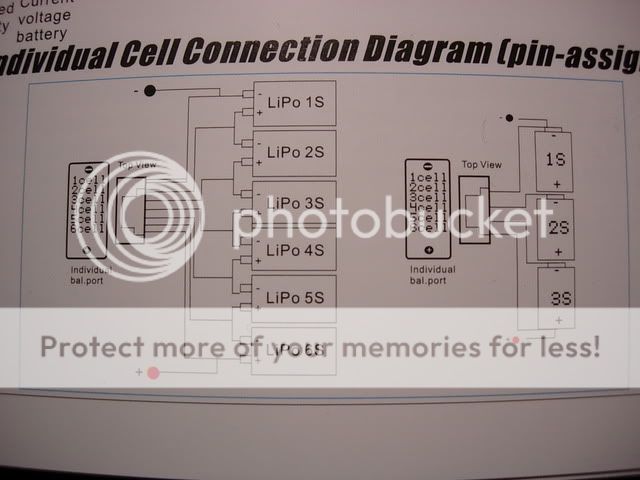
Here is the Wiring Diagram provided in the chargers manual. It lays out for you, pretty clearly (at least to an experienced tech like Me), how to wire up our charge connector. I imagine your charger manual might also feature such a schematic. This particular schematic SHOULD apply to most chargers as the balance Charger connection is a Industry Standard.
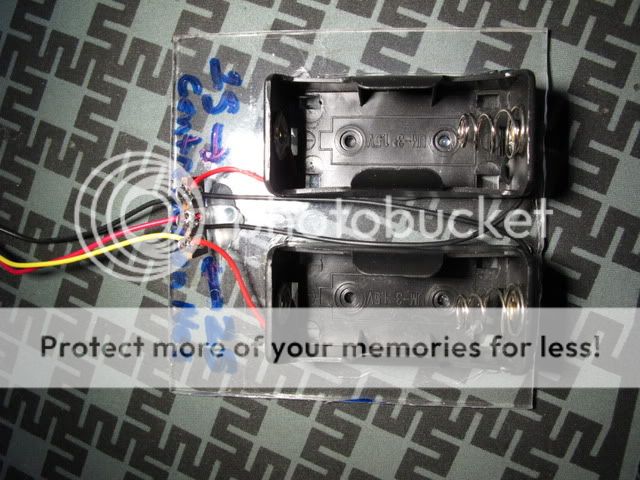
Here is the finished product. I used the centre lug as the common negative, and the adjacent lugs on either side for 1s and 2s connections, then labeled it as such.
If you prefer, feel free to stick to a more linear layout, it's jsut tech instinct to assign the common negative to the mounting lug.
The terminal strip I used is alot smaller then the one use on my 65mm 4s cradle, so I will use caution to make sure the alligator clips do not touch each other or any contacts they are not supposed to.
When sourcing out charge connectors, I recommend getting some that can accommodate the maximum amount of cells you may be building a cradle for. Chances are they will come in a lot.
I got a 10 pack for about $5.
The sockets in my particular charger are backwards compatible, and don't much care how many cells are plugged in at a time, as long as they are in proper order. You can remove extra pins from the connector and tailor it to your needs.
In my case, I bought a lot of 4s connectors off the Bay, and removed two pins to make a 2s connector, and my charger doesn't' mind that it is plugged into the 4s slot.
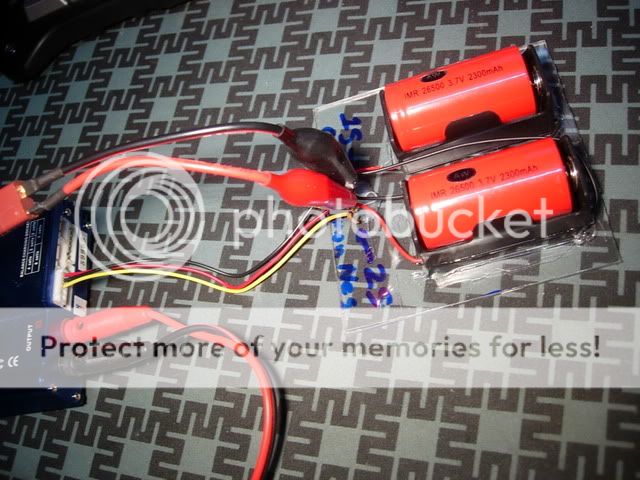
Here I have successfully built a 2 bank charger for my IMR cells.
All parts were sourced from Ebay:
The Battery holders were about 6 for $5.
The connectors were about 10 for $5. Search "balance charger plug".
I forget how much I paid for the Acrylic at Home Hardware.
And the terminal strip could be found in lots for about $1 each. Search: "terminal strips".
One of these cradles likely costs less then 5 dollars. Once you have a lot of supplies as I do, you could build all sorts to accommodate your various battery charging needs.
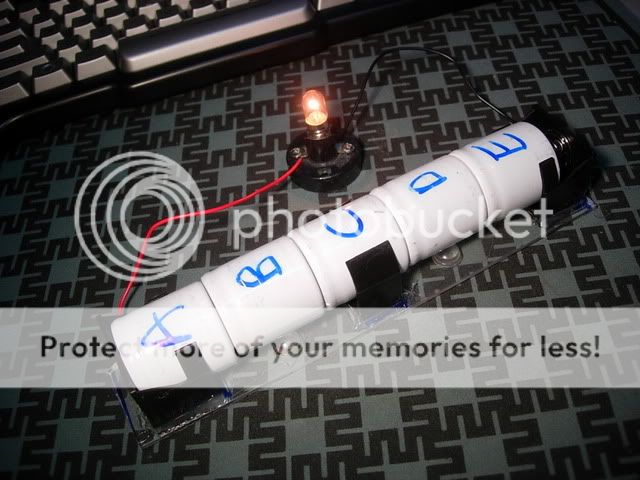
Seen here I chopped a single D-Cell holder, into 3, to create a cradle to charge five 1/2D cells, for dropping 6volts into a 3D Mag, for running Magcharger or Wa1160 bulb.
IMPORTANT SAFETY NOTICE:
These designs have no official safety certification, as such their limits are unknown. It is up to the individual user to verify and monitor their safe operation. Many CPF members will have the experience necessary to construct and safely use these units, and this post is for their benefit.
If used incorrectly or overloaded they could very well pose a fire hazard. For this reason, I advise you build and use one of these units at your own risk.
Unless you have a good idea of the limitations of the particular components used in one of these builds I would recommend limiting the applied current battery holders with stock leads to 1amp. As the leads that came with my battery holders are very flimsy, chances are this current spec will be safe for any other variation of this build.
In use I've noticed some mild warmth coming from the battery holder leads when 2amps is applied. This does not last long, as no matter what current level I would set, the smart charger would throttle down the current to about 1.1amps, and did not seem to want to push any more then that through the flimsy leads.
I can only imagine the charger detected insufficient plumbing and compensated.
Upgrading and Revisions.
If you like this design, and use it regularly . . . AND are confident with your soldering skills, you may consider upgrading the leads to up the charge rate and assure an overall safer operation. I found this necessary as I was unable to get the charge rates I wanted with the stock battery holder leads.
This requires some quick and confident solder welds as the plastic of the holder is likely to melt very easily.
I'm upgrading my cradles using 18 gauge solid wire. The solid wire was chosen mostly for the fact that I already had some on file. Solid wire is capable of conducting more efficiently then stranded wire. As these cradles have a solid frame and don't really need to be shock rated, it's not a bad idea.
18 gauge wire is rate for 3 amps conservatively, and due to the very short distance and low voltages it could easily handle more in this application.
If you are looking to go up to a 10 or more amp charge I would consider using 14 gauge while also rigging it to bypass the stock battery holder contacts as seen here.

Upgrading the positive contacts, I pushed a stripped section of the wire though the battery holders contact holes and bend the exposed section.
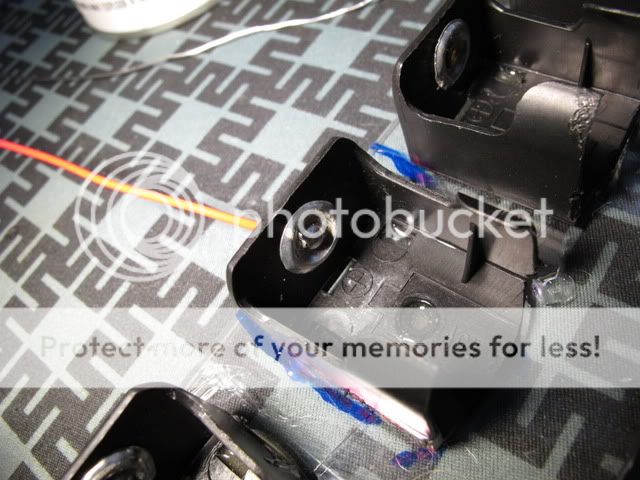
I then pulled the wire back and made a quick solder weld to the contact.
This is the part where you have to be careful as the heat for the weld has likely started the plastic melting regardless of how fast you were.
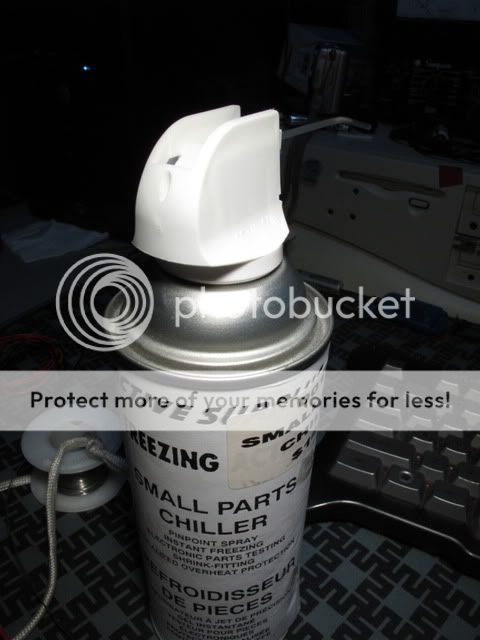
A "tool" handy for this procedure is some "parts chiller" Basically a freezing action spray.
Once I made the weld, while carefully holding everything in place, I took the chiller and sprayed it onto the spot where I had made the weld, solidifying the plastic before it could slip and ruin the holder. You would otherwise have to hold the wire in place until everything cooled down.
If you don't have any boutique parts chiller, you can just use computer "air spray" tilting the can sideways so that the raw liquid sprays out. This is pretty much the same thing as parts chiller.
The other option, if you wish to avoid soldering all together, is once you have the bent wire in place on the inside of the battery holder contact, so simply glue the wire in place on the outside of the holder. I have not tried this personally, but with the right glue and proper technique it could be a good idea.
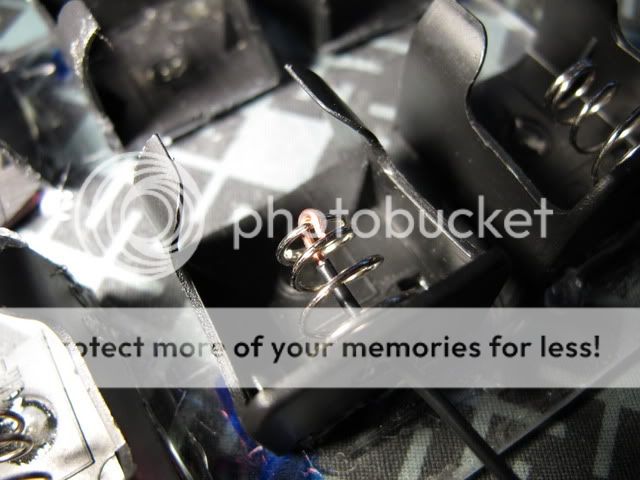
To make the negative contact you pretty much go through the same motions. The difference being that you would pinch the negative wire on the end of the spring like so. This would bypass the spring avoiding any dependency the circuit has on its quality or conductivity.
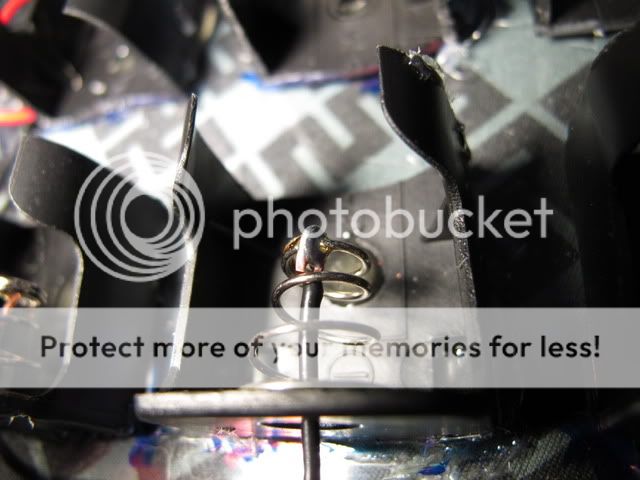
Afterwords, as the spring offers some thermal isolation from the plastic, it is considerably easier to apply solder without the risk of meltdown.
Once again, if you wish to avoid soldering, you can just pinch the wire onto the end of the spring without the need for solder.
Mind you, the solderless methods are likely to work with solid wire only.
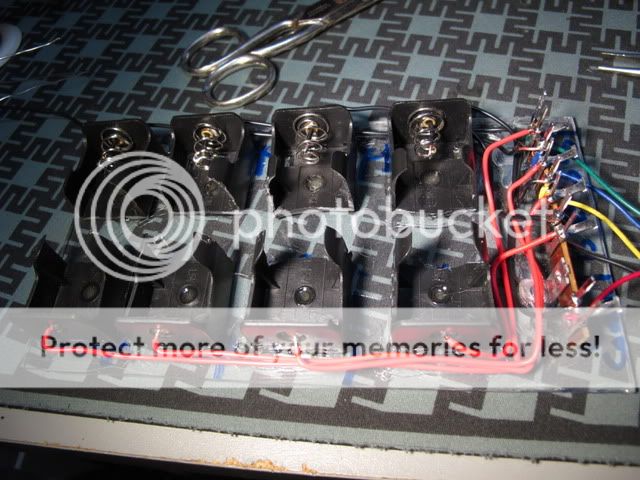
Here we have the revised finished product. I like how the solid wire allowed me to shape it into a more uniform layout.
As discussed in this thread, these particular methods using balance charging systems might be somewhat redundant.
In the case of the 2x50mm cradle, a parallel system might be a better and less complicated way to go.
On the other hand, I find balance charging method advantageous in the 4x65mm cradle when I wish to hit more then 2 cells with a high rate charge. As my particular charger is limited to about 4 amps due to the powersupply used, I would be unlikely to hit 4x26650 LiFe cells with a 1C charge using the parallel method.
The Lux Luthor Magnet Method.
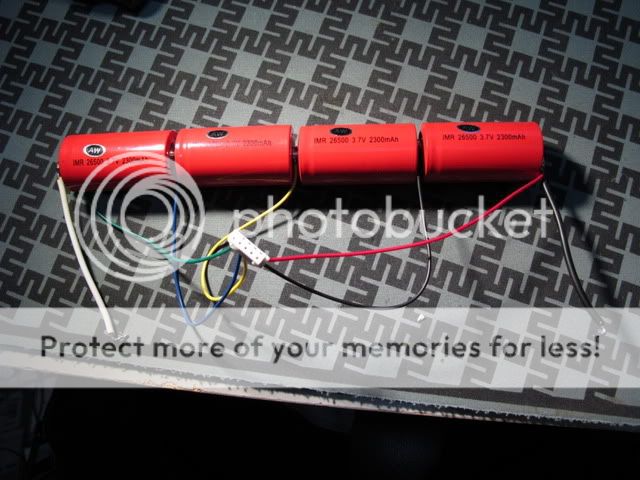
Since the creation of this threat, Lux Luthor brought to my attention another great way in which to utilize the Balance Charging system.
I've decided to try my hand at it.
If you live in Canada, you are likely familiar with the Home Hardware. My local A&J Home Hardware on Bouchard street in Sudbury can be a modders paradise, as they will custom cut you wire or pipe, have a workbench where they help you rough fit projects, and have the stock consistency of a nation wide chain store.
In their limited stationary supply section I was delighted to find they stock just the perfect kind of magnet we need for this project.
As this is a nation wide chain, these magnets should be available, (if by special order) at any home hardware across Ontario, and even Canada I would imagine.
This package cost $7.49cdn +tax.
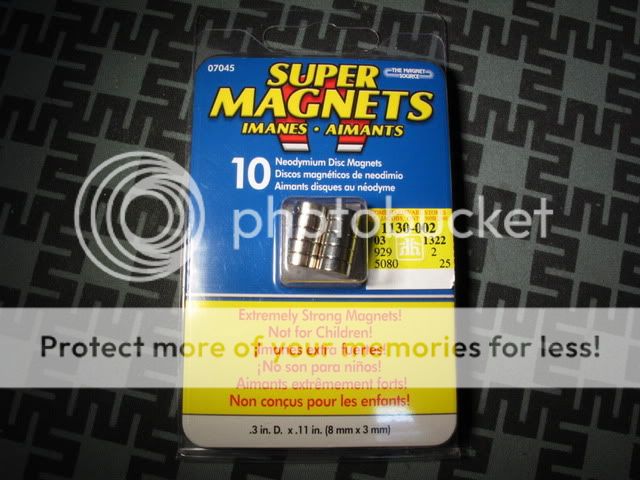
As you can see, I constructed a 4S harness using 6 magnets.
Five for the BC connector (Balance Charge) and the common Negative;
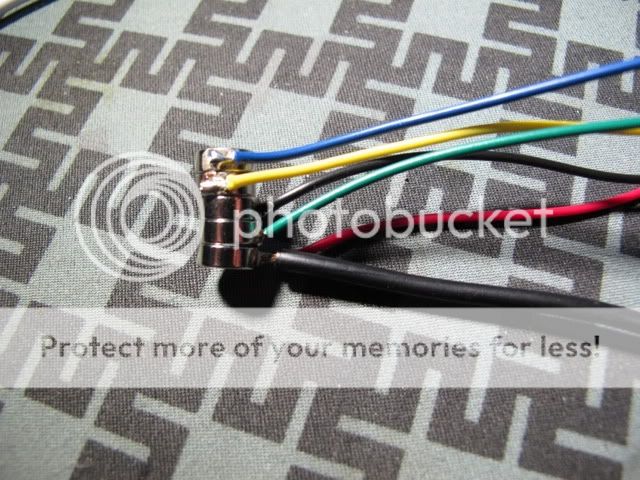
and one for the floating Positive:
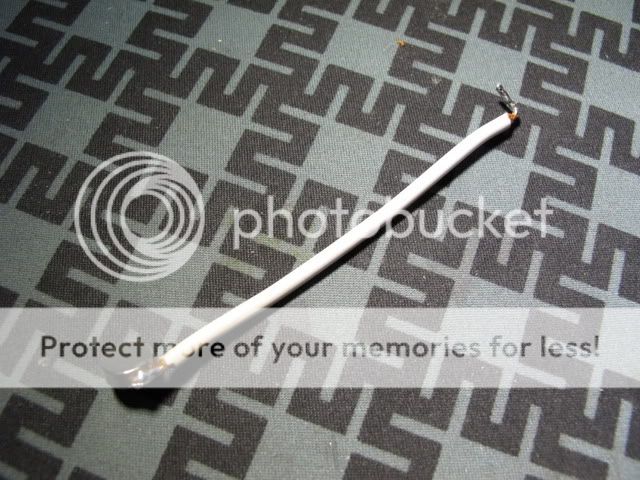
This idea is, you can snap on as many BC connector leads as you need to match your cell count.
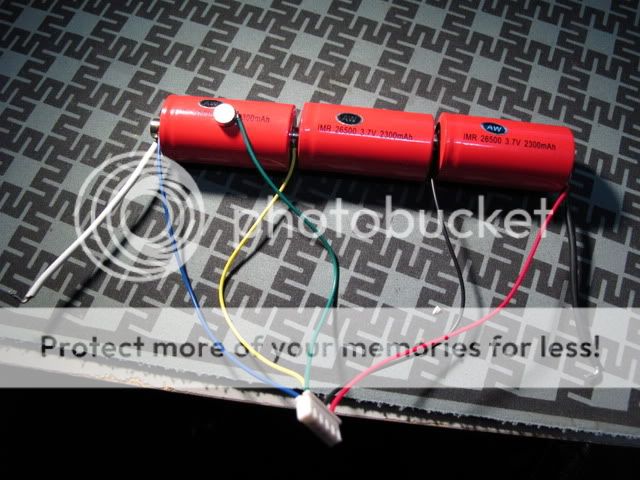
Seen here, I have snapped together 3 cells for the charge. The Blue 3s wire being the last in the chain, snapping the floating posative onto the end of that chain, and omitting the Green 4s lead.
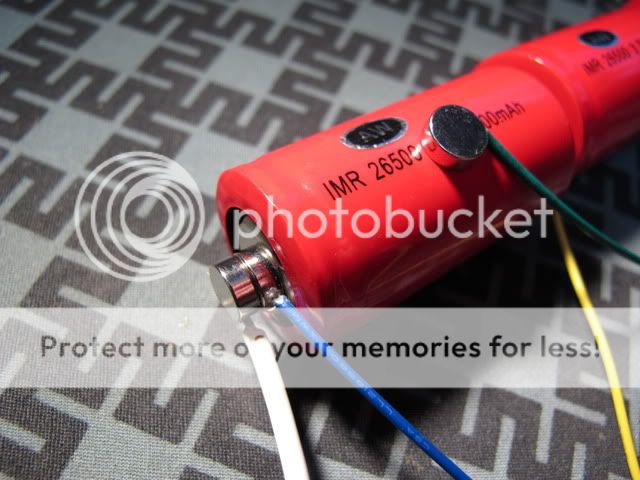
The insulated side of the battery seems a good place to snap the omitted lead magnet. It should stay out of trouble there.
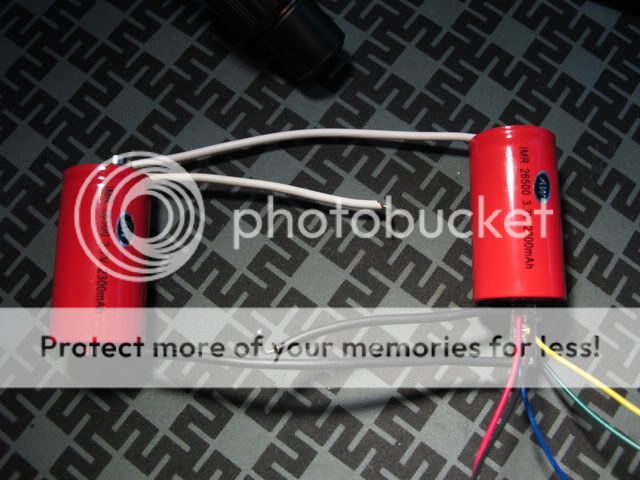
With the remaining Magnets, I soldered up some parallel jumpers so I can use that particular method of charging for a pair of cells.
In this configuration, the omitted magnets are just all snapped together in their standby positions on the negative common side, while the BC connector is not plugged in.
The tricky part of the rig is the soldering. Too much heat applied to the Magnet can strip it of its magnetization rendering it useless. I've known this for a while. It's common knowledge among competent guitar techs that the use of high output soldering guns has been known to demagnetize electric guitar pickups.
Lux has mastered it, and has dropped tips among the forum. I myself have been soldering for over 16 years, and have the right equipment, so though reluctant to damage the magnets, I figured I could handle it.
The trick is to be quick, avoiding to much iron time on the magnet. You pretty much have to know how to solder and have decent experience doing so.
Refer to the "Butter on Toast" tip mentioned earlier in the thread. In this case, imagine using a blow torch to heat the bread just enough so that the butter melts into it, but without actually toasting it.
The method is something to be seen. I have made this HD video to illustrate.

If you can do the motions as seen here, you should be able to pull it off.
What you are seeing is:
A: I "tin" and preheat the wire for soldering,
B: I tin and preheat the magnet surface ",
C: I fuse the preheats and tinned parts together,
D: I quickly spray some "chiller" on the magnet to remove all access heat.
Tinning in the process of pre-fusing some solder onto the surfaces to be connected, as you would with contact cement glue, or even epoxy.
It's pretty much a mandatory prerequisite to making a good solder joint.
For tools:
- I have a set of jaws or "helping hands" to hold everything,
- A 35watt soldering iron. Note the medium flat tip used. Too sharp a tip might not spread the heat evenly. To wide may spread it too much making it hard to focus your
heat and overheating the magnet. The right tip could make or break this joint, you should be good with a fine tip though. A 35-45 watt iron with a med flat tip is pretty much a swiss army knife of irons to those who can use them well. DO NOT, use a solder gun!
- Some FINE standard Rosin Core solder. Nothing special but the size. Too thick could flood your joint making for a sloppy work.
- Parts chiller. The chiller has been discussed already, look for the pic of the can.
I was able to pull this off in one shot with no damaged magnets.
If you are not confident doing this, I would practice on some random pieces of metal. Maybe try soldering to the edge of a penny as they are about the same mass as the magnets, just keep in mind, It will take about half the time to fuse to the magnet as it would to the penny. I would recommend soldering to the edge of the magnets as it will take longer for the heat to spread across then it would if you soldered to middle. For soldering the common negative, fuse the main lead and the BC lead together before welding to the magnet so that you only have one joint to make.
Last but not least, mind the polarity. When you stack the magnet, they will only snap together one way, if you want your wires to be oriented a certain way, best to figure out how they will snap together before making the connections.
ENJOY !
Last edited: