So, I squished some Cree XR-E emitters the other day, mentioned here: https://www.candlepowerforums.com/threads/223988
Today, I decided to do some experimenting. I desoldered them from their star modules, and attacked one with some serious scissors. The ceramic substrate on those suckers is HARD! But I was able to lop the corners off, which was my goal.
Why remove the corners of the substrate? Because that's where the vias are! I want to eliminate the thermal resistance of the star module by soldering my emitter directly to the heatsink. This requires either milling channels in the heatsink to run wires into, or somehow disconnecting the electrical contacts on the underside of the substrate. The latter is the course I took.
The vias are clearly visible here:
After desoldering the emitter and trimming the corners off, I verified with a meter that the bottom contacts no longer connected to anything. Then I soldered wires to the topside contacts and tested it:
My theory thus confirmed, I then scuffed a nice clean area onto the end of some copper stock, added a bit of flux, and applied plenty of heat:
Success! The emitter is soldered directly to the copper bar but both contacts are electrically isolated from it. I can now buy bare emitters rather than star modules, mount things in ways stars wouldn't allow, and enjoy a more direct thermal path. I can use pre-1982 pennies instead of star modules if I need convenient slugs for more elaborate mounting.
Full-res photos and mouseover annotations at http://flickr.com/photos/myself248/
Today, I decided to do some experimenting. I desoldered them from their star modules, and attacked one with some serious scissors. The ceramic substrate on those suckers is HARD! But I was able to lop the corners off, which was my goal.
Why remove the corners of the substrate? Because that's where the vias are! I want to eliminate the thermal resistance of the star module by soldering my emitter directly to the heatsink. This requires either milling channels in the heatsink to run wires into, or somehow disconnecting the electrical contacts on the underside of the substrate. The latter is the course I took.
The vias are clearly visible here:

After desoldering the emitter and trimming the corners off, I verified with a meter that the bottom contacts no longer connected to anything. Then I soldered wires to the topside contacts and tested it:
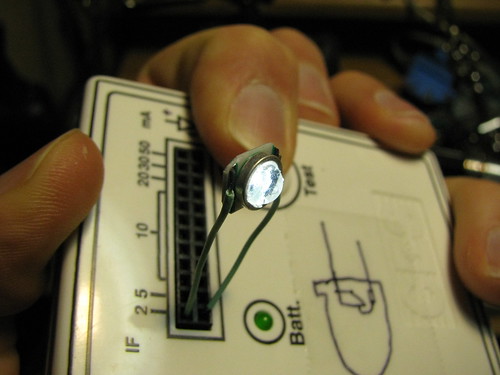
My theory thus confirmed, I then scuffed a nice clean area onto the end of some copper stock, added a bit of flux, and applied plenty of heat:
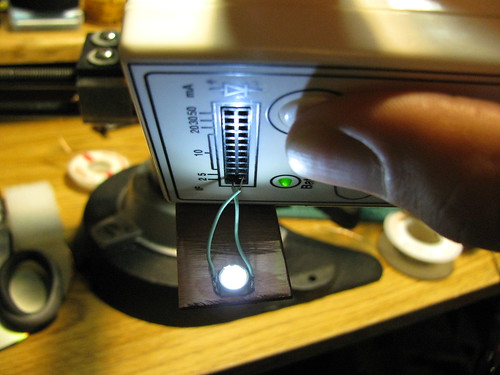
Success! The emitter is soldered directly to the copper bar but both contacts are electrically isolated from it. I can now buy bare emitters rather than star modules, mount things in ways stars wouldn't allow, and enjoy a more direct thermal path. I can use pre-1982 pennies instead of star modules if I need convenient slugs for more elaborate mounting.
Full-res photos and mouseover annotations at http://flickr.com/photos/myself248/