archer6817j
Enlightened
Hi folks,
I've been talking to some MCPCB manufacturers about making custom 2mm thick copper core boards to use in my custom lights.
I just saw the "thermal path" thread and realized I should ask the experts here to get some advice and to make sure I'm getting my money's worth from the manufacturer.
First of all, my application has some limitations and I won't be able to create the "ideal" thermal situation but I want to make it as good as possible with what I've got to work with.
I've also been updating my testing methods to the ANSI standard for output. The good news is that @ 3 mintues the output is stable. The bad news is, I'm loosing about 100 lumens compared to the "@ turn on" output. I'd like to get this loss down as much as possible. Here are the constraints:
1) I'm using a solid head (no pill) and the LED is inserted from the front of the head. The surface immediately behind where the LED is mounted is 3/8" of aluminum...but keep in mind the head is solid.
2) I'm using thermal tape with no screws, but following the manufacturer's recommendation for pressure and time. I know this isn't as good as arctic silver and screws but the main reason I'm doing this is that the screws interfere with the optics I'm using (and most optics I've tried). So, I decided the best way to increase the thermal efficiency is to go with a copper MCPCB vs. an aluminum one.
3) the MCPCB thickness will be 2mm. This is the thickness of my current aluminum MCPCBs and I can't go any thicker without altering the dimensions of the head. However, it seems like 2mm should be a "decent" thickness considering the copper stars from KD (or wherever) are around .8mm
4) the star size is 20mm
So, given the above, do you have any thoughts or advice on the physical design of the board with respect to trace layout, circuit layer thickness, dielectric layer thickness, etc?
Is this something people would be interested in purchasing as a component? The cost is quite high at a volume of 100 pcs...say in the neighborhood of $15 just for the MCPCB (not including the LED).
Let the games begin!
I've been talking to some MCPCB manufacturers about making custom 2mm thick copper core boards to use in my custom lights.
I just saw the "thermal path" thread and realized I should ask the experts here to get some advice and to make sure I'm getting my money's worth from the manufacturer.
First of all, my application has some limitations and I won't be able to create the "ideal" thermal situation but I want to make it as good as possible with what I've got to work with.
I've also been updating my testing methods to the ANSI standard for output. The good news is that @ 3 mintues the output is stable. The bad news is, I'm loosing about 100 lumens compared to the "@ turn on" output. I'd like to get this loss down as much as possible. Here are the constraints:
1) I'm using a solid head (no pill) and the LED is inserted from the front of the head. The surface immediately behind where the LED is mounted is 3/8" of aluminum...but keep in mind the head is solid.
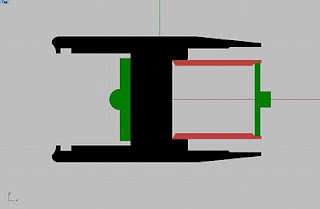
2) I'm using thermal tape with no screws, but following the manufacturer's recommendation for pressure and time. I know this isn't as good as arctic silver and screws but the main reason I'm doing this is that the screws interfere with the optics I'm using (and most optics I've tried). So, I decided the best way to increase the thermal efficiency is to go with a copper MCPCB vs. an aluminum one.
3) the MCPCB thickness will be 2mm. This is the thickness of my current aluminum MCPCBs and I can't go any thicker without altering the dimensions of the head. However, it seems like 2mm should be a "decent" thickness considering the copper stars from KD (or wherever) are around .8mm
4) the star size is 20mm
So, given the above, do you have any thoughts or advice on the physical design of the board with respect to trace layout, circuit layer thickness, dielectric layer thickness, etc?
Is this something people would be interested in purchasing as a component? The cost is quite high at a volume of 100 pcs...say in the neighborhood of $15 just for the MCPCB (not including the LED).
Let the games begin!