Walterk
Enlightened
Another thought.. why haven't I seen this around yet ....
You would loose the losses within the star and this will divide the heat over the heatsink faster.
Paste or grease will fill any void if you use a bleedhole.
Soldering the led can be done before mounting the post.
A key to turn the post can be made by making a cut in a strip of steel, overstressing the copper is the hardest part, don't make the thread in the aluminium to narrow.
You will need a cheap set of threadmaking tools and a vice, but you wont be depending on a lathe machinist for making a proper thermal connection.
And the aluminium sink would have to have a certain mininimum thickness, say 10-15mm to make the effort worthwhile ?
Find rod
Bore and thread sink
Thread rod
Dry fit rod and cut rod to size and file/Dremel slot for Led/key
Solder led and wires
Mount post with TIM
Done
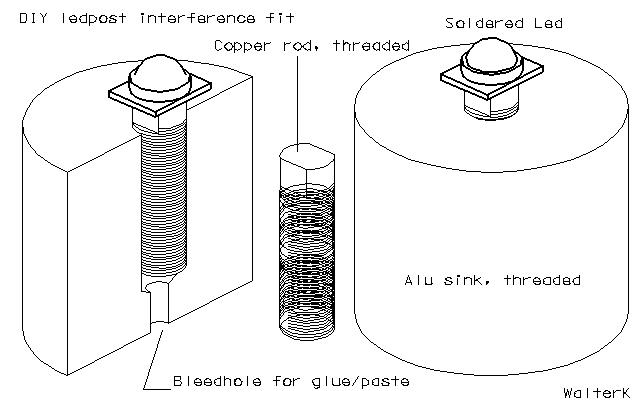
You would loose the losses within the star and this will divide the heat over the heatsink faster.
Paste or grease will fill any void if you use a bleedhole.
Soldering the led can be done before mounting the post.
A key to turn the post can be made by making a cut in a strip of steel, overstressing the copper is the hardest part, don't make the thread in the aluminium to narrow.
You will need a cheap set of threadmaking tools and a vice, but you wont be depending on a lathe machinist for making a proper thermal connection.
And the aluminium sink would have to have a certain mininimum thickness, say 10-15mm to make the effort worthwhile ?
Find rod
Bore and thread sink
Thread rod
Dry fit rod and cut rod to size and file/Dremel slot for Led/key
Solder led and wires
Mount post with TIM
Done
Last edited: