Late in the summer I started playing with Anodizing. My thought was to save money and machine my own parts vs buying a bunch of Maglites.
A number of DIY sites provide various methods and details for the process and tools required.
To power the process some people suggested computer power supplies, Car batteries with incandesant light bulbs, others suggested battery chargers, and yet others just said to buy a power station.
So I:
Burned out 2 old power supplies.
Spent a day getting frustrated with the charger... turns out the newer models are too smart for me... they won't power up if they don't detect some current from a battery in the first place.
Tried a car battery but wasn't thrilled.
End result was... I bought a bunch of Mags.
Last night I was a bit bored, still waiting Cutter!, so I started researching the Anodizing process again...
when a Light went off... (bad pun)
To properly Anodize we need Constant Current.... well DUH same with LEDs
Having just gotten a new H6CC from Taskled I decided to wire something up
Using a 14.4 (4s x 18650) battery pack, the HC66 set to 6A, and a 15% Sulphuric Acid solution
I successfully anodized the tube shown on the right and dyed it gun metal gray.
The aluminum part on the left is not anodized for comparison.
It's harder, colored and shows 0 Ohms.....
I've just ordered some dyes for my next build!
A number of DIY sites provide various methods and details for the process and tools required.
To power the process some people suggested computer power supplies, Car batteries with incandesant light bulbs, others suggested battery chargers, and yet others just said to buy a power station.
So I:
Burned out 2 old power supplies.
Spent a day getting frustrated with the charger... turns out the newer models are too smart for me... they won't power up if they don't detect some current from a battery in the first place.
Tried a car battery but wasn't thrilled.
End result was... I bought a bunch of Mags.
Last night I was a bit bored, still waiting Cutter!, so I started researching the Anodizing process again...
when a Light went off... (bad pun)
To properly Anodize we need Constant Current.... well DUH same with LEDs
Having just gotten a new H6CC from Taskled I decided to wire something up
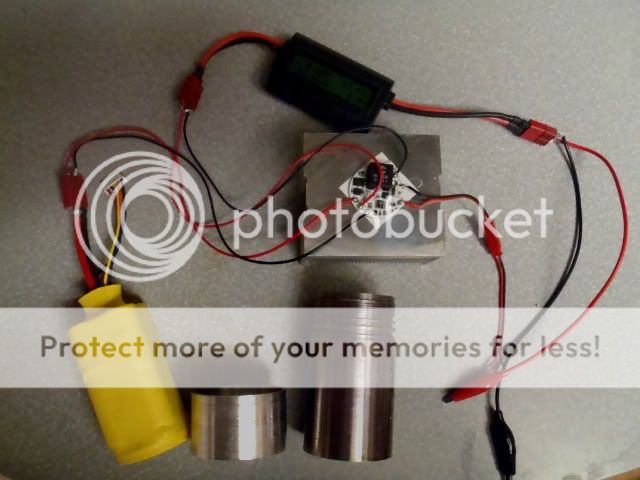
Using a 14.4 (4s x 18650) battery pack, the HC66 set to 6A, and a 15% Sulphuric Acid solution
I successfully anodized the tube shown on the right and dyed it gun metal gray.
The aluminum part on the left is not anodized for comparison.
It's harder, colored and shows 0 Ohms.....
I've just ordered some dyes for my next build!